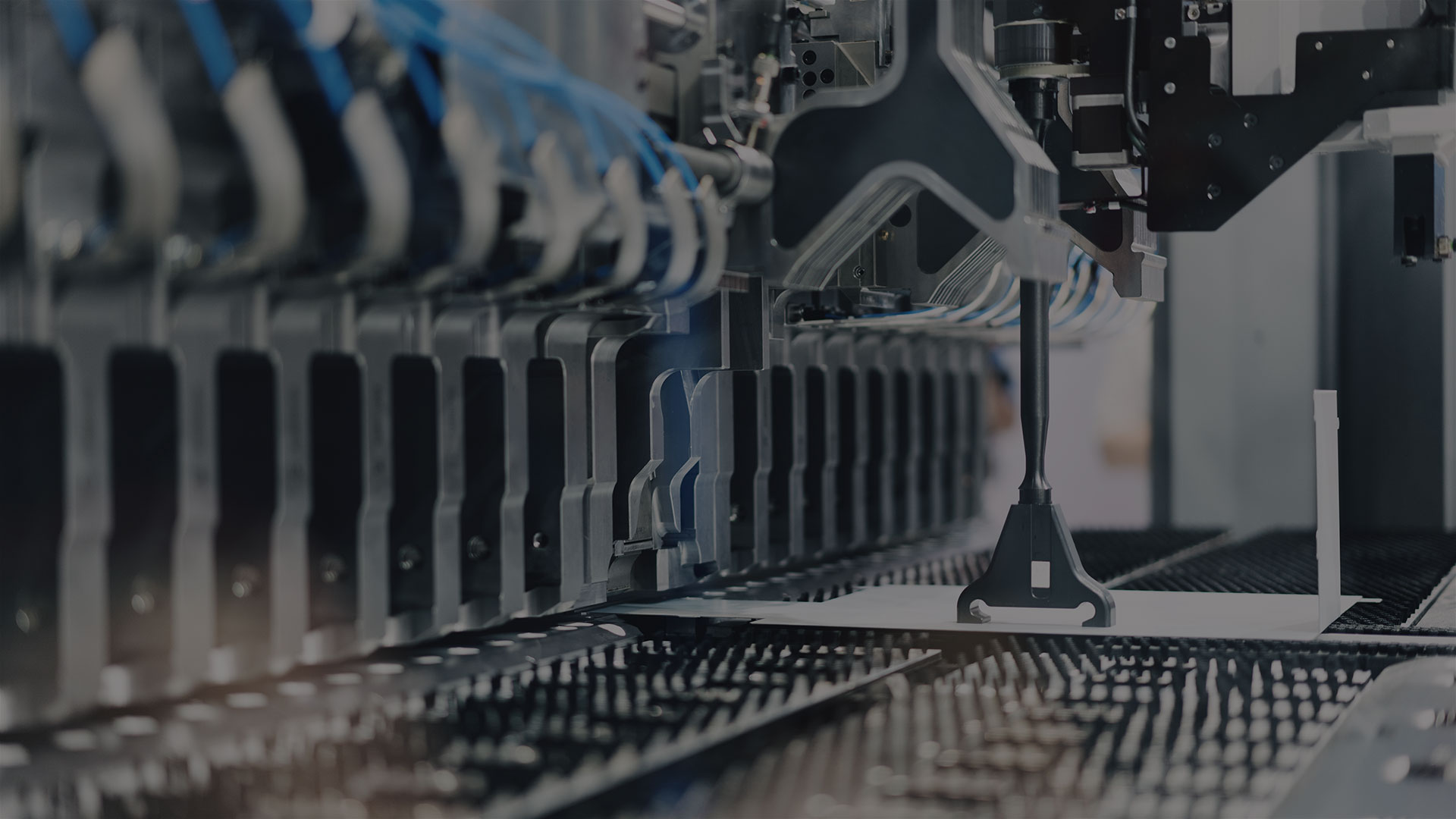
What the Fourth Industrial Revolution Means for Manufacturing
While the term “Industrial Revolution” may conjure images of European cities in the early 1800s, there have actually been several throughout modern history. The history of digitization is long, winding, and continues to unfold today. The most recent, which is still underway, is the fourth industrial revolution, sometimes referred to as “Industry 4.0,” and is largely tied to the Internet of Things and how powerful new interconnected technologies like cognitive automation, machine learning, and artificial intelligence are rebuilding the way businesses operate.
We’re already seeing many organizations across industries undergo extensive digital transformations to capitalize on the benefits new technologies can offer. According to a 2018 Tech Pro Research survey, 70 percent of companies either have a digital transformation strategy in place or are working on one. However, given the high-tech nature of Industry 4.0, especially compared to previous industrial revolutions, it might seem like manufacturing businesses won’t be as involved. In fact, the manufacturing industry has just as much to gain from these new digital solutions.
Way Manufacturers Can Implement Digital Solutions
Here are a few ways manufacturing businesses can utilize digital solutions and business automation technologies powering the fourth industrial revolution:
Optimization of Supply Chains: The biggest benefit of Industry 4.0 can be summed up in one word: connection. Thanks to the Internet of Things - the integration of an increasing number of “smart” technologies continuously feeding new data to an expansive network - businesses are able to streamline their supply chains and develop more efficient processes. Manufacturers can leverage this interconnectedness to accommodate changing economic conditions and other unexpected events that may otherwise hamper their business. When unforeseen circumstances cause shipments to be delayed, a smart system powered by this trove of data and navigated by AI and machine learning can proactively adapt and modify manufacturing priorities.
Streamlining Internal Processes: The Internet of Things can be leveraged to improve the efficiency of manufacturing businesses’ internal processes as well. Manufacturing may be a more physical business than most other industries, but there are still plenty of tasks and operations that take place in cyberspace. Many of these can be sped up and done more accurately by advanced robotic process automation (RPA) programs. Any repetitive, rules-based tasks are ideal for RPA.
Autonomous Equipment: Rows of large autonomous robotic arms manning assembly lines where they efficiently and quickly assemble various parts and products have become something of a poster-child for business automation in general. Once, these machines were expensive, and extremely specialized - each capable of only performing one task or series of tasks for which they were specifically programmed. Thanks to advances in design and software, similar robots are now capable of learning many tasks, and even solving for more efficient ways of completing problems posed to them. At the same time, they’ve gotten less expensive and more accessible to small and medium-sized businesses.
3D Printing: Additive manufacturing, more commonly known as 3D printing, has come a long way in the last few years. This technique was once only used for small-scale, small-batch items and creating simple prototypes is now maturing into an actual scale production option. And with advanced AI and ML systems, manufacturers can identify and implement improvements not only in their processes, but in the very designs they use as well. Products can be built more durably with less material and greater efficiency, giving manufacturers that embrace Industry 4.0 a significant edge.
How to Prepare Your Business for Industry 4.0
So, clearly, there are plenty of ways manufacturing businesses stand to benefit from the 4th industrial revolution. But how can you ensure that your business does so effectively? Here are 3 important first steps:
1. Identify Use Cases
There may be many ways Industry 4.0 can be leveraged, but that doesn’t mean that all of them apply to your specific business. That’s why the most important first step you can take is to identify realistic use cases for business automation within your company. Keep in mind, you don’t necessarily want something flashy. There’s a good chance the digital solution that will drive the most value for your company will be mostly behind the scenes. Automating internal processes is a great way to realize significant returns and enable downstream integrations as you begin to automate more parts of your business.
2. Get Internal Agreement
One of the biggest challenges of adopting any new technology is always getting buy-in from internal stakeholders. Even the most carefully chosen opportunities for business automation won’t succeed if you don’t first get buy-in from leadership and the workers whose day-to-day workflows will be impacted by the change.
It can be helpful to conduct employee surveys and assessments to get a sense of overall sentiment towards business automation before moving forward with a selected upgrade. It’s also worth sharing information internally, whether through emails, presentations, or in-person meetings, regarding how new digital solutions will impact processes. Hands-on training is a critical part of the implementation process to encourage adoption and clearly demonstrate the new technology’s value to relevant stakeholders.
3. Consolidate Databases
The essential fuel for the fourth industrial revolution is data. Cognitive automation, AI, and machine learning all require quality data inputs to reach their greatest potential. That’s why one of the most effective ways to prepare your business for a swift and easy adoption of the latest smart technology is centralizing and organizing your data.
Consolidating all datasets may not be practical for all businesses. In those cases, federated search solutions that allow users (and automated systems) to access multiple disparate data sources all from one search can achieve a similar result.
As business automation and the fourth industrial revolution continue to advance, the operational benefits they offer will continue to grow in tandem. Businesses that neglect to update their systems and adapt to the new technologies will soon find themselves at a serious disadvantage. It’s important to learn about these new technologies, identify how your business might stand to benefit, and lay some groundwork for a smooth implementation to ensure your business is able to adapt, survive, and thrive in Industry 4.0. To get started on digital transformation, learn more about Exela's digital solutions for manufacturing.